Facebook details robot-based aerial fiber deployment method
Facebook Connectivity, via a blog on the Facebook Engineering website, has provided details of the fiber deployment technology for use on aerial power line networks it unveiled early this year (see “Facebook says it has a better way to deploy fiber-optic cable”). The approach uses a specially designed robot that runs along a medium voltage power line, wrapping fiber cabling around it. The technique can lower the cost of aerial fiber deployment to $2.00 to $3.00 per meter, Facebook asserts. The company plans to conduct trials of the deployment method next year.
The blog’s author, Facebook Wireless Systems Engineer Karthik Yogeeswaran, said the idea for the new approach came from seeing the relative ubiquity of power line infrastructure in rural Africa. The company was inspired to find a way to leverage these power lines as a foundation for fiber deployment as a means of increasing communications availability in such rural areas. The company researched various approaches, alongside an array of partners, before settling on this one.
For example, Facebook decided to adapt the helical wrap method already used to deploy fiber-optic cabling around an existing power-line conductor. However, conventional machinery for this approach would be too bulky, require too much human intervention, and weigh too much for use on the targeted infrastructure. Much of the weight problem derives from the use of spools of high-count fiber cable. Facebook determined that 24-fiber-count cable would be adequate to their needs. However, the stresses and thermal conditions inherent in medium voltage power lines rendered conventional fiber inadequate. To solve this issue, Facebook consulted with longtime fiber cabling designer Wayne Kachmar (currently partnered with Fiber Optic Center; see “Fiber Optic Center partners with Northern Lights Cable founder for consulting services”), working with partner companies and academic advisors, to develop a specialized cable design. The cable uses G.657 200-micron fibers with a specially tailored aramid configuration and a high-strength, high-temperature, track-resistant polymer jacket.
Meanwhile, the typical use of a spool presented logistical headaches, so Facebook eventually adapted a technique, originally designed for military use, that comprises a spool-free cable coil geometry. The approach meets the clearance requirements around the power line conductor to enable the robot to pass obstacles on the line while maintaining a center of mass aligned within 2 mm of the center of the power line. The lack of a spool and the otherwise necessary counterweight decreases the weight of the robot while remaining balanced on the line as it clears obstacles such as the power line conductors.
The robot was designed by ULC Robots to require a minimum of human interaction. A full deployment would require two or three linemen and a pickup truck carrying fiber spools, the robot, and what Yogeeswaran termed “a few accessories.” One of these is a mechanism, developed by Quanta Services, to get the robot on and off the power lines.
Facebook estimates that a robot could deploy more than 1 km of fiber cable (1 km is the design load) in an hour and a half. However, taking into account set up and other factors, Yogeeswaran says his employer estimates that a robot could deploy 1.5 to 2.0 km of fiber cable a day.
Once the approach is proven, Facebook will turn it over to NetEquity Networks, which has been granted a royalty-free license to use the robot-based technique in fiber deployments.
For related articles, visit the Network Design Topic Center.
For more information on fiber cable and suppliers, visit the Lightwave Buyer’s Guide.
To stay abreast of fiber network deployments, subscribe to Lightwave’s Service Providers and Datacom/Data Center newsletters.
About the Author
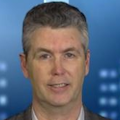
Stephen Hardy
Editorial Director and Associate Publisher, Lightwave
Stephen Hardy is editorial director and associate publisher of Lightwave and Broadband Technology Report, part of the Lighting & Technology Group at Endeavor Business Media. Stephen is responsible for establishing and executing editorial strategy across the both brands’ websites, email newsletters, events, and other information products. He has covered the fiber-optics space for more than 20 years, and communications and technology for more than 35 years. During his tenure, Lightwave has received awards from Folio: and the American Society of Business Press Editors (ASBPE) for editorial excellence. Prior to joining Lightwave in 1997, Stephen worked for Telecommunications magazine and the Journal of Electronic Defense.
Stephen has moderated panels at numerous events, including the Optica Executive Forum, ECOC, and SCTE Cable-Tec Expo. He also is program director for the Lightwave Innovation Reviews and the Diamond Technology Reviews.
He has written numerous articles in all aspects of optical communications and fiber-optic networks, including fiber to the home (FTTH), PON, optical components, DWDM, fiber cables, packet optical transport, optical transceivers, lasers, fiber optic testing, and more.
You can connect with Stephen on LinkedIn as well as Twitter.